Progressing Cavity Pump Technology
Learn everything you want to know about PCP technology.
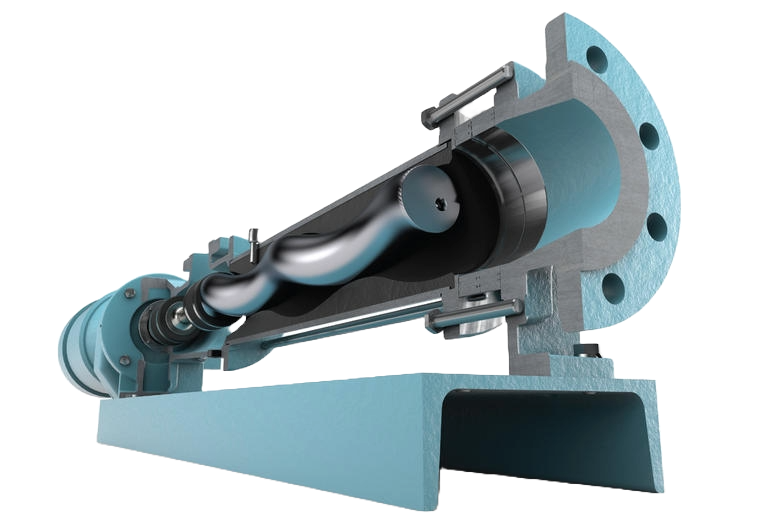
Definition
What are Progressing Cavity Pumps?
Progressing Cavity Pumps (PCP) are high-quality, reliable and efficient pumping solutions designed for a wide range of applications. Known for their rugged construction and precise technology, these pumps are ideal for industries such as wastewater treatment, pulp and paper, chemical processing, food and beverage, and more.
With their unique design, these pumps provide continuous flow with low pulsation, unaffected by pressure and viscosity fluctuations. They are also self-priming and capable of handling high solids and abrasive materials. Easy to maintain and available in a variety of sizes and configurations, these pumps can be tailored to meet specific requirements.
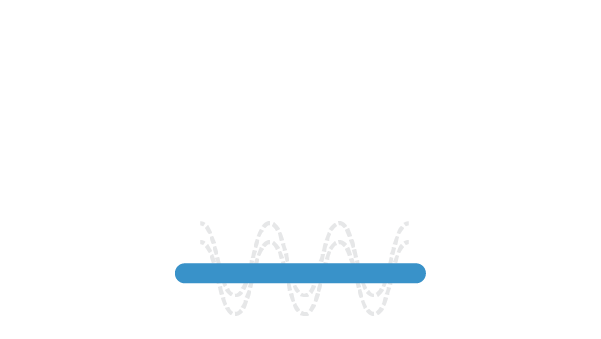
Precise & Gentle Transport
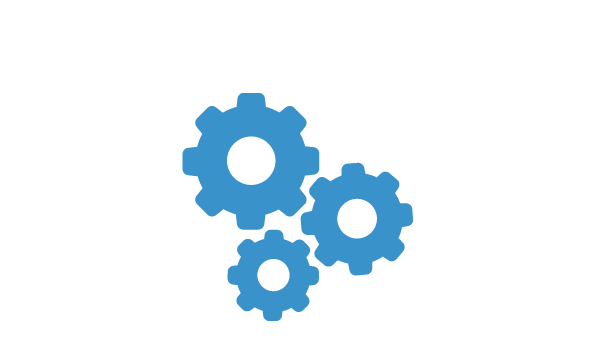
Long Lasting Stators
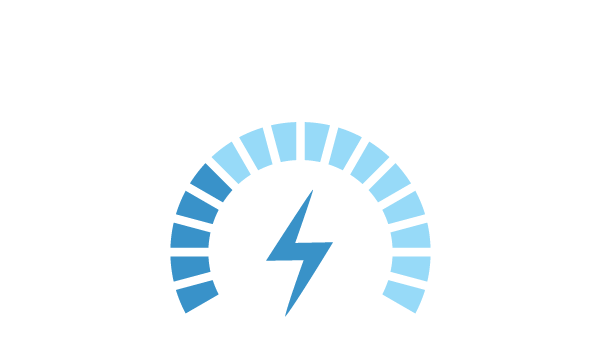
Energy Saving
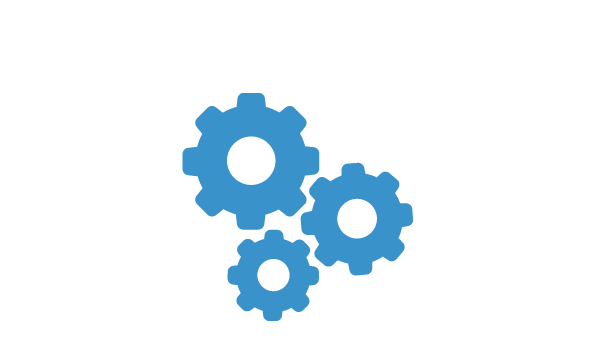
Low Maintenance
Technology
How do Progressing Cavity Pumps work?
Progressing cavity pumps are rotary positive displacement pumps used to transfer liquids. The technology behind these pumps lies in the unique design of the pump components, which essentially consist of an eccentrically rotating screw called a rotor and a stationary stator.
The ROTOR, usually made of steel or stainless steel, is often referred to a helical shaped screw with a defined pitch. The STATOR has a complementary helical geometry and has always one thread more than the rotor and is usually made of a flexible elastomer vulcanized into a metal tube. As the rotor rotates inside the stator, it creates sealed cavities that move from the suction to the discharge end of the pump, allowing the fluids to be pumped.
PCP technology provides a constant flow rate proportional to speed, regardless of the pumping pressure. This makes it an excellent product for applications involving high-viscosity, solid-laden or shear-sensitive fluids.
Another feature of progressive cavity pumps is their ability to handle fluids of varying viscosities, from aqueous to nearly solid. They can also handle aggressive, corrosive and abrasive fluids and overcome high system pressures, making them suitable for a wide range of industries, including oil and gas, mining, food processing and wastewater treatment.
Progressing Cavity pump technology offers energy efficiency advantages because the pumping process has minimal internal slippage and turbulence, reducing energy losses. The pumps can also operate at relatively low speeds, which reduces wear and extends pump life. Another advantage of the low speeds, combined with the resulting pumping chambers, is that the pumped media are conveyed extremely gently and without shear effects. The fluids remain homogeneous and there is no turbulence or swirling.
Watch the video to see how progressing cavity pumps work.
Benefits
Advantages of Progressing Cavity Pump Technology
ALLWEILER progressing cavity pumps offer a number of advantages that make them the preferred choice in many industries, including wastewater treatment, food processing, chemical and pharmaceutical, and more.
For power transmission and eccentric movements within the rotating unit, the pump requires a drive shaft that ends in encapsulated pin joints at both ends. In Allweiler pumps, these are particularly simple and robust, and absorb the eccentric movement of the rotor trouble-free.
No other pump is as space efficient as this optimized design. It results in uniquely long service intervals (MTBF) because power is transmitted through replaceable, hardened bushings and pins. They reliably protect the other joint components from wear and can be easily replaced. The joints of Allweiler progressing cavity pumps are durable, oil-lubricated, solids-tight and overpressure-resistant.
The Allweiler design eliminates the need for an axial seal on the joint, which can quickly wear and/or be damaged by the constant movement of the components and any solids that may be present in the pumped fluid. Only a radial seal is required to seal the joint. The joint's protective metal shroud effectively deflects solids around the joint, providing additional protection.
The wear-resistant joint sleeves surround the joint and are held in place by two retaining straps. Allweiler joints are oil lubricated, and the movement of the joint and the associated forced circulation of oil provide optimum lubrication and long service life.
Allweiler's block pumps feature a self-sealing, rust and dirt resistant connection between the drive and the pump. Quick and easy assembly and disassembly. Approximately 30% smaller shaft diameter, resulting in up to 50% less friction on the shaft seal. This results in less wear, longer life and lower replacement costs.
The bearing frame can be removed from the drive shaft as a complete unit. The shaft seal is accessible without further pump disassembly. The bearing bracket can be relubricated and the bearings are protected from splash water.
The innovative rotor geometry results in a 20% lower average sliding velocity, resulting in lower energy consumption (less drive power) and longer rotor life.
Patented process eliminates grooves and creates a shark-skin surface structure. Your benefit: Lower static and sliding friction, resulting in lower motor power and starting torque. Shaft seals last longer and require less motor power because the smaller diameter of the stub shafts reduces seal friction by approximately 50%.
The innovative honeycomb structure of our progressing cavity pumps allows the liquid phase of the pumped liquid to be absorbed by the stator surface. This minimizes hydrodynamic drag for greater efficiency and energy savings.
This technology, also inspired by nature, allows us to reduce the internal friction of the pump by up to 50% compared to conventional progressing cavity pumps. Reduced start-up and operating torques allow operators to move more fluid with significantly less effort and energy consumption.
The combination of the honeycomb structure and the shark's skin ensures a nearly frictionless flow with no turbulence, resulting in a smooth flow rate and a stable performance curve during operation.
All Allweiler rotors and stators are manufactured in-house in Germany. This ensures consistent, superior quality for these critical components that determine pump performance and efficiency.
For stators, we have the ability to select the right elastomer from over 20 materials suitable for different media. In addition to the standard elastomers, Allweiler also offers Alldur®, a unique elastomer material. Our ALLDUR® stators offer up to five times longer service life, even with abrasive media.
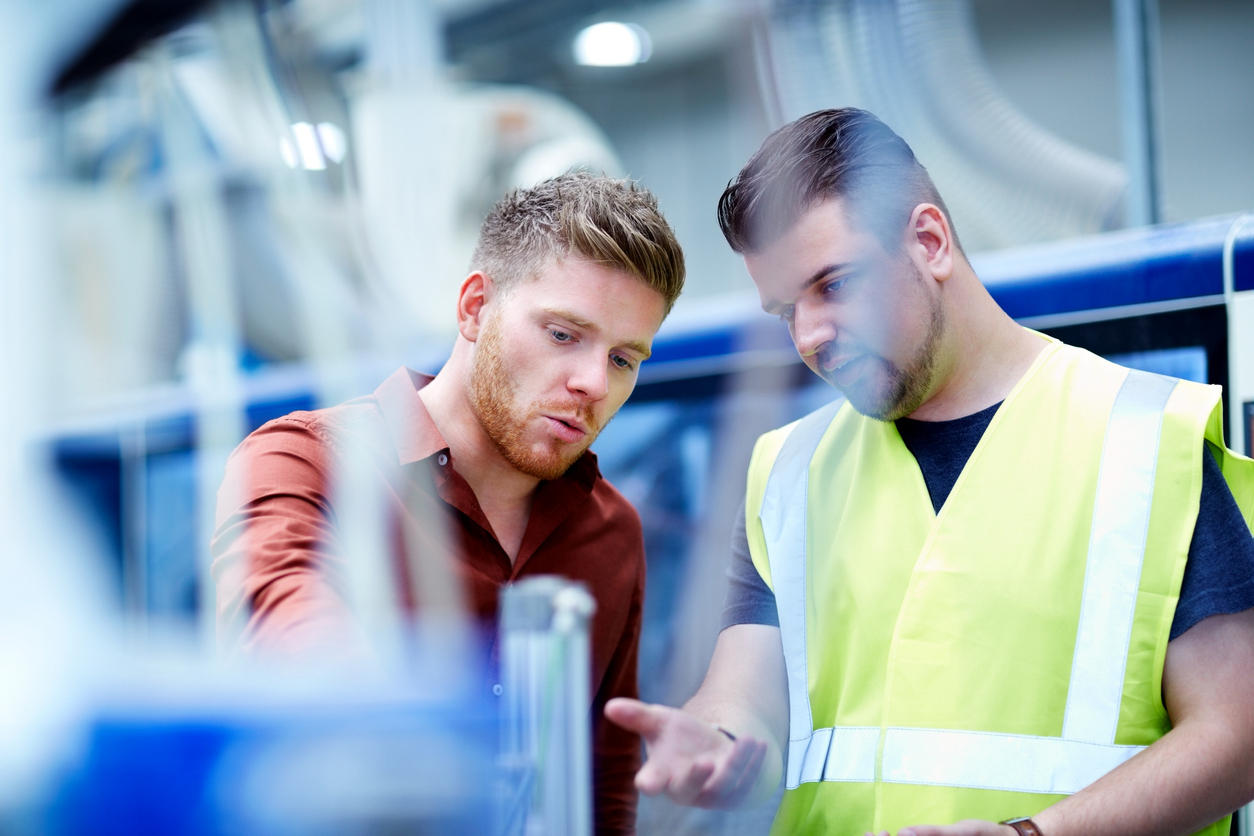
Support
How to choose the right Progressing Cavity Pump
Due to the variety of models in our diversified product portfolio, selecting the right PC Pump requires experience. Several factors are important: Fluid properties, operating conditions, environmental conditions, the overall system and applicable standards and regulations. Finding the right, cost-effective PC Pump that matches to the process requirements best can be a challenge.
Our team of experts helps to make the right choice.
We will work with you to review your application and determine which pump meets your needs best.
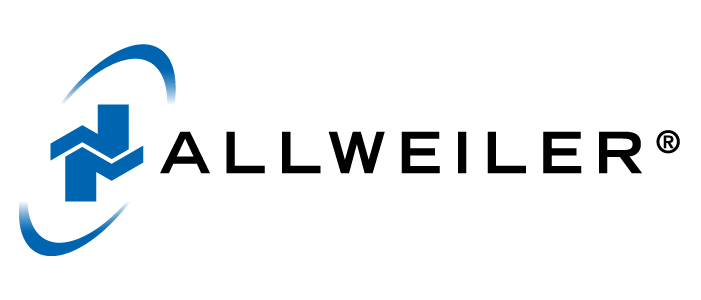
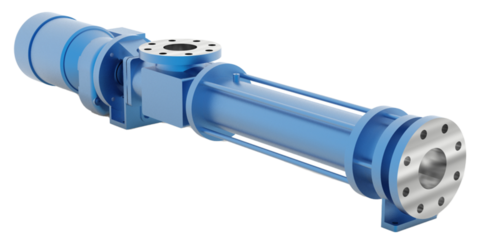
Developed for multiple pump series, this technology offers incredibly fast disassembly and assembly times and provides best-in-class Mean Time To Repair (MTTR). Suitable for a wide range of fluids.
1.600
Max. Discharge Pressure [bar] :10
Max. Fluid Temperature [°C] :100
Max. Viscosity [mm²/s] :190.000

For dosing and handling high-viscosity, solids-laden fluids. We have combined proven and durable features from our proven industrial pump range with optimized rotor and stator geometries to ensure the highest dosing accuracy.
33
Max. Differential Pressure [bar] :24
Max. Fluid Temperature [°C] :100
Max. Viscosity [mPas] :28.000
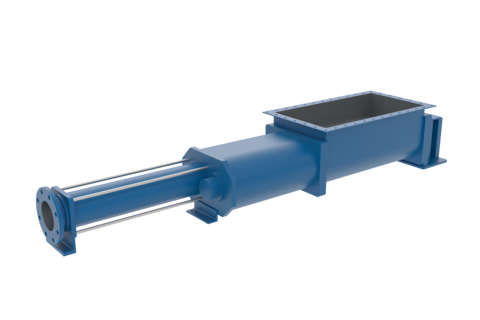
For handling viscous, abrasive or solids-laden materials in various industrial applications. Their unique hopper design enables efficient and smooth product transfer in this tough environment.
1.700
Max. Differential Pressure [bar] :36
Max. Fluid Temperature [°C] :135
Max. Solid Content [%] :45
Max. Viscosity [mm²/s] :1.000.000
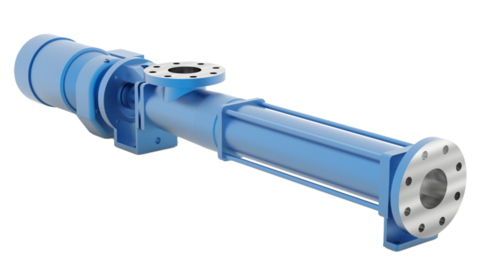
Optimizes all hydraulic characteristics such as flow pattern, power absorption and distribution, and lubrication to ensure long service life and maximum efficiency.
3.800
Max. Discharge Pressure [bar] :6
Max. Fluid Temperature [°C] :135
Max. Viscosity [mm²/s] :300.000