Three-Screw Pump Technology
Learn everything you want to know about the advanced technology.
Dive into the unique design and gain comprehensive insights into their efficiency and reliability. Setting new standards in fluid handling.
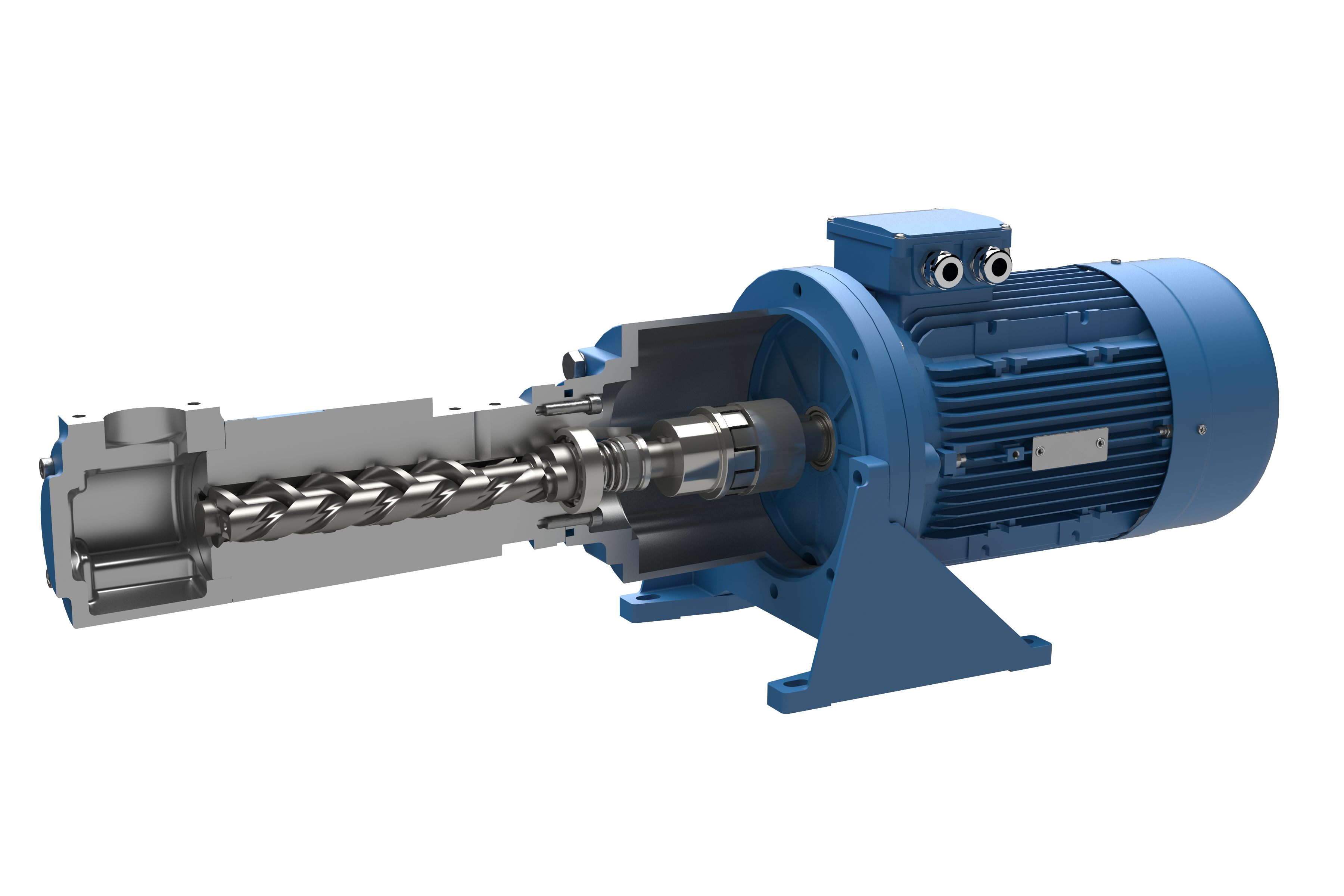
Definition
What are Three-Screw Pumps?
Screw-Pumps with three spindles, known as Three-Screw pumps, are part of the screw-pump family. They are characterized by high power density and great versatility thanks to their compact design. Thanks to the unique design with three intermeshing screws, they provide extremely efficient and uniform flow, resulting in impressive overall efficiency.
Screw-Pumps in general are true all-rounders. They can handle a wide range of fluids, viscosities (0.3 to 100,000 cSt), gas contents (up to 100 %) and abrasive media. They are characterized by excellent controllability with nearly constant efficiency over a very wide operating range (flow and pressure). As with volumetric displacement pumps, the flow rate is determined by speed and is not dependent on pressure, density or viscosity.
The self-priming three-screw pumps offer not only the excellent controllability of volumetric positive displacement pumps, but also minimal pulsation and remarkably quiet operation even at high discharge pressures (>100 bar).
Their robust design and high wear resistance of the spindles ensure reliability and long service life. This makes Three-Screw pumps the ideal choice not only in their traditional application for clean, medium to good lubrication fluids such as lubricating oils or mineral oil-based fuels, but thanks to the use of advanced materials and manufacturing technologies also for non-lubricating, corrosive and/or abrasive fluids such as seawater or chemicals.
Technology
How do Three-Screw Pumps work?
Three-Screw pumps are part of the family of positive displacement pumps. They are equipped with a drive spindle and two auxiliary spindles housed in a liner.
A Special profiling of the screw flanks allows the three spindles to form sealed chambers. The fluid inside is axially and continuously displaced from the suction to the discharge side of the pump as the spindles rotate. The discharge pressure is built up uniformly over the entire length of the spindles. The gap between the rotating spindles and between the screws and the liner is designed for minimum backflow, ensuring pulsation-free, uniform pressure build-up in the screw chambers and optimum hydrodynamic support for the spindles. There is no turbulence despite spindle rotation. The steady rotating volume in the chamber prevents crushing forces.
The Three-Screw pump is known for its uniform, pulsation-free flow, high pressure capability and high efficiency. It is also very quiet and low in vibration, making it suitable for a wide variety of applications, preferably with lubricating media such as hydraulic oil, lube oil or fuel, but in special versions also with demanding non-lubricating and/or abrasive media.
Watch the video to see how three-screw pumps work.
Benefits
Advantages of Three-Screw Pumps Technology
Three-Screw pumps are extremely versatile and efficient pumps that can be used in a wide variety of applications. Here are some of their key advantages:
Three-Screw pumps are known for good suction characteristics. It allows to evacuate air from the suction pipe and prime the liquid, allowing to start pumping without the need for external priming. They also have very low NPSHr values. This feature greatly simplifies operation and system design.
Unlike gear pumps and oscillating displacement pumps such as piston or diaphragm pumps, Threw-Screw pumps deliver the fluid very smoothly and continuously, eliminating pulsations. The fluid is handled gently, without acceleration, turbulence or squeezing. Since pressure pulsations can damage a system and its components, this contributes significantly to increased plant availability. Complex, expensive pulsation compensators are not required, and plant vibrations are reduced.
The screw profile creates a continuous, smooth flow which, in addition to low pulsation, results in very low airborne and structure-borne noise emissions. These are up to 15-20 dB lower than those of conventional gear pumps, for example. The noise emission of a Screw-Pump is therefore typically much lower than of the electric motor powering it.
Thanks to the hydrodynamically supported operating principle of the spindles, in which the pressure builds up over the entire length of the spindles, Three-Screw pumps operate with extremely low wear and are known for their long, low-maintenance service life. There is only one seal and one bearing. This makes the pumps very easy to maintain.
Our three-screw pumps can handle a wide range of fluids with different viscosities - from low-viscosity fluids as low as 0.3 cSt to high-viscosity fluids up to 10,000 cSt. Pump performance is not affected by the density of the fluid being pumped. This versatility makes them suitable for applications involving a wide range of fluids in a variety of industries.
Three-Screw pumps are highly efficient, ensuring that a significant portion of the drive power is converted into usable hydraulic energy. Smooth, turbulence-free flow, close tolerances between the spindles and the liner, and low axial acceleration of the fluid result in minimal internal backflow, resulting in maximum efficiency.
Three-Screw pumps feature a compact design with high power density, making them ideal for applications where space is limited. This is ideal for efficient integration into systems or equipment.
Unlike centrifugal pumps, the Three-Screw pump does not have a Best Operating Point (BOP), but can be operated over a very wide performance range with almost constant efficiency. Because of the linear pump curve, the flow rate of a Screw-Pump can be easily controlled by speed. The pressure adapts to the process requirements. It is also well suited for a variety of changing fluids with different densities, viscosities, flow rates and pressure requirements.
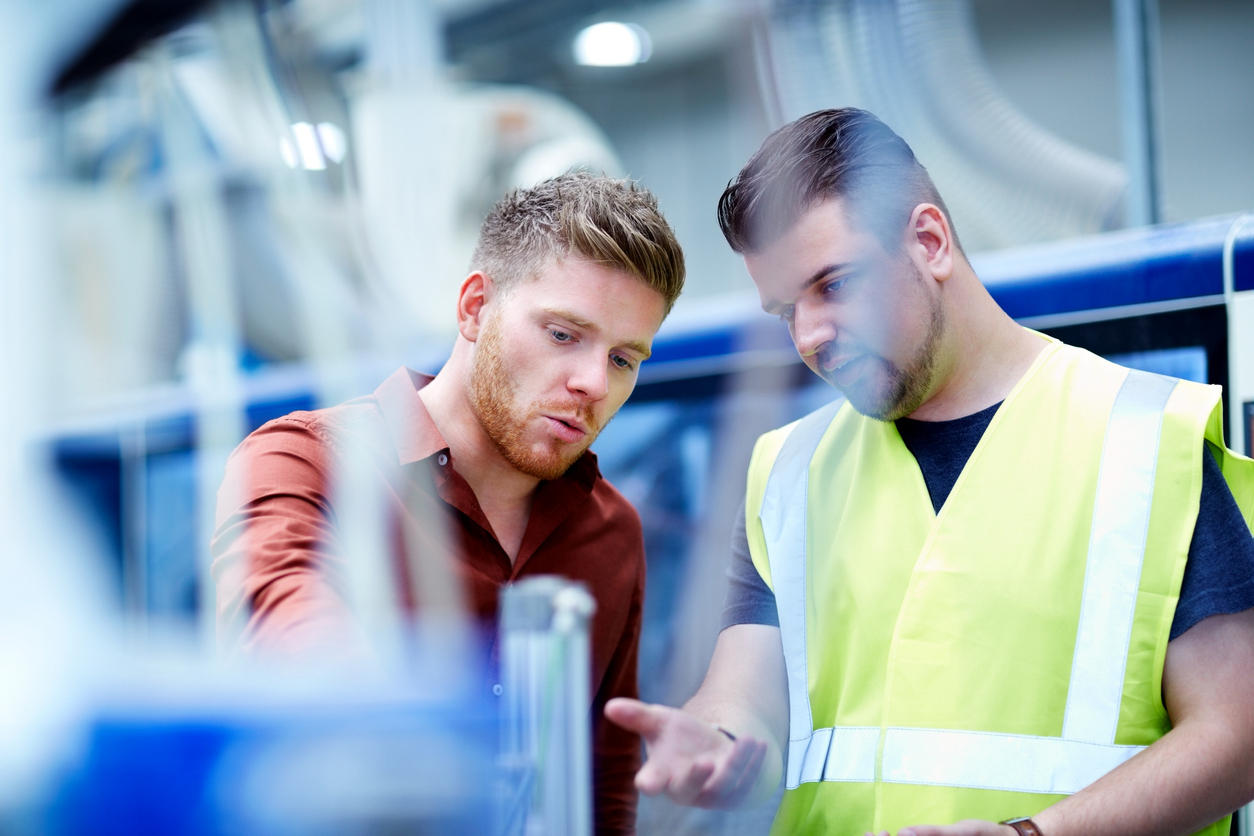
Support
How to choose the right Three-Screw Pump
Due to the process-optimized variety of models, selecting the right Three-Screw pump requires experience. Several factors are important: Fluid properties, operating conditions, environmental conditions, the overall system and applicable standards and regulations. Finding the right, cost-effective Three-Screw pump that matches to the process requirements best can be a challenge.
Our team of experts helps to make the right choice.
We will work with you to review your application and determine which pump meets your needs best.
Trusted Brands
Three-Screw Pumps from ALLWEILER & IMO
Choosing CIRCOR's Allweiler and IMO Three-Screw pumps offers many benefits to the customer. The Allweiler and IMO brands are industry leaders. Being the inventors of Three-Screw pumps back in the early 1920s, our brands have millions of installations globally.
Our pumps are designed to deliver maximum performance in a wide range of applications, ensuring versatility to meet diverse customer needs. In addition, our global network of sales and service partners provides excellent customer service, technical support and advice to help customers select the right pump for their needs. This ensures optimal performance. Because we understand the importance of our pumps to our customers' systems, we ensure very long spare parts availability.
You can also take advantage of our global manufacturing facilities in the U.S., Germany, India and China, which ensures that pumps are available close to you. Because we care about the environment, our pumps are designed and manufactured in an environmentally responsible manner. All pumps are designed to minimize environmental impact through their durability, ease of maintenance, efficient operation and use of environmentally friendly materials.